ABSTRACT
A database program called WorkPlan has been created to systematically develop weekly work plans. Such work plans are used by crew foremen in scheduling work packages and allocating available labor and equipment resources. WorkPlan adopts the Last Planner methodology, which implements several lean con- struction techniques. A week prior to conducting work, WorkPlan guides the user step by step through the process of spelling out work packages, identifying constraints, checking constraint satisfaction, releasing work packages, and allocating resources; then at the end of the week, collecting field progress data and reasons for plan failure. This systematic approach helps the user create quality work plans and learn from understanding reasons for failure. The lean planning philosophy underlying WorkPlan and the functionality of the computer program implementation are detailed in this paper. Various ways of displaying work package data are illustrated. WorkPlan’s job-shop scheduling view complements the view traditionally adopted by project management, as is reflected in scheduling tools using the critical-path method.
INTRODUCTION
Scheduling of construction work is usually done with the support of computer tools that implement the critical-path method (CPM). These tools have served project managers well in their effort to plan and oversee construction projects in the process of administering contracts. They also have presented a common representation (based on activities of given duration and unit resources allocated to them, as well as predecessor relationships between activities) for different parties involved in a construction project to communicate with one another who should be doing what work and when. However, these tools are inadequate in terms of use and expressiveness when it comes to supporting production planning and control, that is, supporting those who are performing construction work in the field.
The ability to actually get work done at the construction work face depends on the availability of resources. Resource availability must be checked prior to starting the work. Resources relevant to field workers, namely erection drawings, materials, equipment and tools, available work space, and methods specifications, rarely, if ever, are explicitly described in CPM schedules. Using CPM, one can allocate resources to activities, however, CPM does not make it easy to specify and check prerequisite resources. A CPM user could add a predecessor activity, one for each prerequisite. Not only is it tedious to do so, it also requires a different mindset, not to mention that the activity network would explode in size. Project management's schedules are therefore useless to those doing the work.
Accordingly, field workers developed their own special-purpose planning systems called weekly work plans, but they have done so with varying degrees of success. Although systems tend to differ from one company to the other, the information in them is usually work-to-be-done, people and equipment assigned for specific days or hours, and materials needed. Even though actual resource allocation and checking is done in preparation of the weekly work plan, resources do get cross-allocated or over-allocated, resulting in conflict. This occurs because there is no easy mechanism to verify resource assignment when the weekly work plan is spelled out on paper.
Therefore, the biggest problem field workers face is coping with discrepancies between anticipated, actually needed, and available resources. Numerous uncertainties (e.g., ambiguities in design drawings, errors in take-off, fabrication errors requiring rework, delays in shipment, damage during handling, etc.) affect the flow of resources prior to their application. Shielding field workers from that uncertainty by means of proper planning is key to minimizing impact on their productivity.
This issue is addressed in this paper first by presenting a crew-level planning system that implements such a shielding method in order to overcome this deficiency in current practice with regard to weekly work planning. More importantly, lean construction techniques have been implemented in a database application called WorkPlan. WorkPlan systematically guides users through the steps required for creating a quality work plan. Its underlying data-checking mechanism helps maintain data consistency. WorkPlan allows the data to be organized in various ways for accounting purposes and to display performance measures.
TRADITIONAL APPROACH TO PROJECT SCHEDULING
Weekly work planning is planning with the highest level of detail prior to having (skilled) laborers carry out the work. Actual resource allocation and checking is done in the preparation stage of the weekly work plan. Currently, most weekly work plans are drawn up by hand, using pen and paper. If a work package spans more than one week, its description will have to be rewritten each time a new plan is made, week after week. Also, information regarding laborers and equipment required in multiple work packages will have to be duplicated from one form to the next. Most paper-based weekly work plans are discarded after they have served their purpose: crew supervisors use them as ‘‘crib sheets’’ to sequence work, assign work, and mobilize resources. Russell and Froese (1997), therefore, referred to such plans as ‘‘throw-away’’ schedules. The opportunity for supervisor or management feedback and learning is thereby lost.
In addition, weekly work plans bear little relationship to the CPM of the project. More surprisingly, they are not used to track labor hours spent (time cards) or the completion of work. Once construction has been carried out, progress is recorded in time sheets. Resources used are assigned to cost accounts to manage project expenditures (e.g., pay for labor), which also requires paying attention to detail.
The irony of this practice is that weekly work plans and time sheets essentially contain the same information, namely work to be done for a given week, though one looks one week into the future and the other looks one week back. Nevertheless, two separate forms are typically used, and there appears to be no explicit relationship between them. Tying the two together is the missing link between production and project management.
The traditional construction management approach is to define activities and schedule work to be done, prior to the start of construction, in terms of what SHOULD be done. Activities are identified, timed, and sequenced so as to best serve the project objectives. The mental attitude driving this type of scheduling is ‘‘can-do.’’ It means that those doing the work (i.e., production crews) are being committed by management to doing (WILL) whatever the schedule says SHOULD be done, with no real consideration for what they are actually able to do (CAN) at any specific point in time. RESOURCES simply are assumed to be available when needed so that SHOULD presumably is do-able and guaranteed to result in DID. After the schedule has been determined, and as construction progresses, it is up to those production crews to gather what resources they have on hand and to adhere to the schedule as well as they can.
The can-do attitude is rooted in the fact that the person or organization responsible for producing the schedule does not have a clear understanding of the work to be performed. Because they lack the hands-on experience, they cannot clearly define the full scope or assess the real nature of the work to be done, methods to be used, and required capacity of resources to be applied. Thus, work cannot be planned at the level of detail that is required to optimally perform it and control production. Therefore, the workforce has traditionally been told what goals to accomplish, and it was left up to them to determine how to accomplish those goals, even though the means to achieve them may be beyond their control. The reality is that the schedule reflects only anticipated resource availability, but actual resource availability can differ substantially from it, so crews are bound to deviate from that original schedule.
The limitations of the can-do mind set are made clear in Figs. 1 and 2. In the traditional approach to planning, SHOULD would point directly to ‘‘Executing the Plan’’ (Fig. 1). Now consider that planning means selecting from what SHOULD be done to complete a project, and deciding for
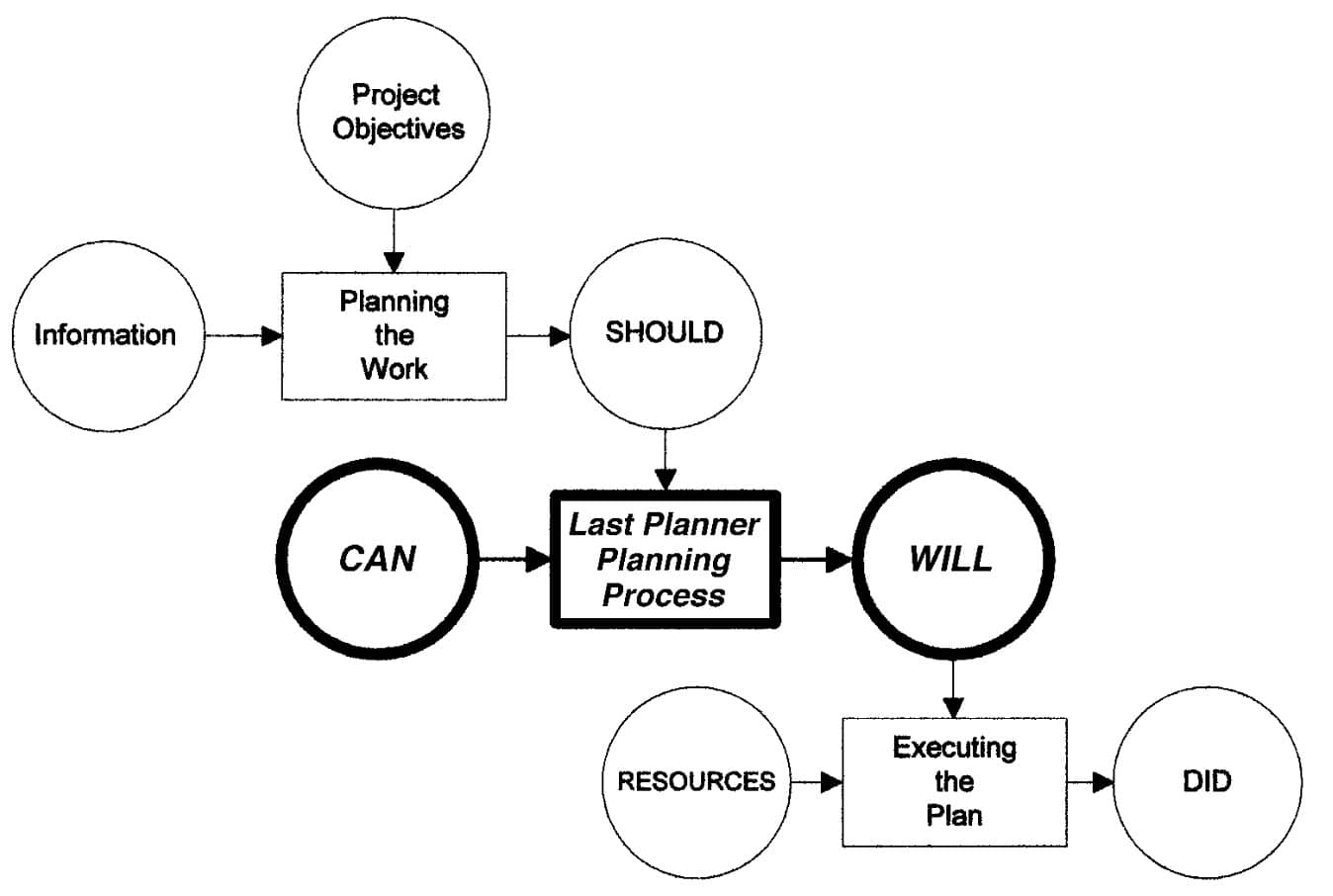
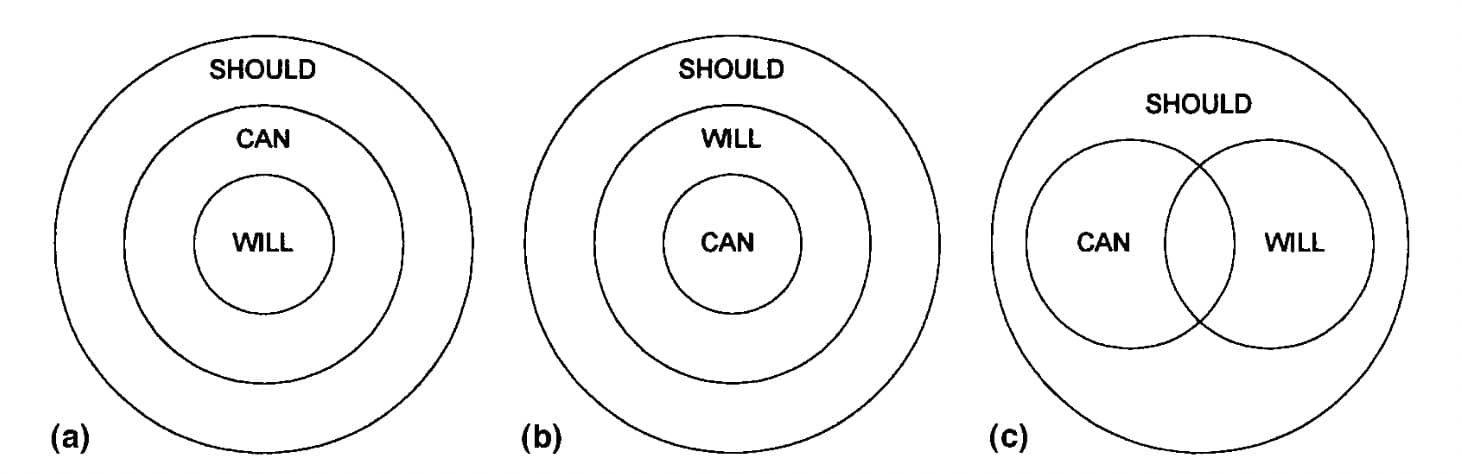
given time frames what actually WILL be done. Because of resource constraints, not all CAN be done. Compare situations A and B [Figs. 2(a and b)]. In situation A, a subset of what SHOULD be done CAN be done, and a subset of what CAN be done WILL be done. Accordingly, there is a high likelihood for what has been planned (WILL) to be successfully completed (DID). Note that 100% success is never guaranteed as unforeseen plan execution failures may occur (e.g., due to machine breakdown or accidents).
In situation B, CAN is a subset of WILL. While commitments (WILL) may have been made during planning, not all CAN be successfully pursued, so the plan is doomed to fail (DID differs from SHOULD). Most construction projects, however, are best characterized by situation C. CAN and WILL both are subsets of SHOULD, but they overlap only partially with each other. The plan typically is developed (WILL) without knowing what CAN be done, and it is left up to the production crews to find out what intersection exists between the two when they try to execute the plan.
THE LAST PLANNER
Finding out what CAN be done at the time work is to be performed not only is a time-consuming endeavor, it also defeats the very purpose of planning. We therefore propose that the crew perform a last step in planning—whence ‘‘The Last Planner’’ (the term denotes both the method as well as the person who applies the method)—a reasonable time (e.g., a week) prior to performing work. This step enables them to identify what part of the work that SHOULD be done CAN be done, and then commit (WILL) to doing only that work. The resulting Last Planner’s schedule thus reflects what WILL be done, CAN be done, not simply what SHOULD be done. Fig. 1 illustrates the Last Planner process that must precede schedule execution to result in DID.
The Last Planner’s plan must be developed shortly before performing work, e.g., during weekly work planning. Choosing what work field workers WILL perform in the next week from what they CAN perform is termed ‘‘making quality assignments.’’ The reason for making only quality assignments is to shield the production crew from uncertainties in workflow. Ballard and Howell (1998) propose that weekly work plans are effective when assignments meet specific quality requirements for:
Definition: Are assignments specific enough so that the right type and amount of materials can be collected, work can be coordinated with other trades, and it is possible to tell at the end of the week if the assignment has been completed?
Soundness: Are all assignments workable? Are all materials on hand? Is design complete? Is prerequisite work complete? Note that make-ready work will remain for the foremen to do during the week, e.g., coordination with trades working in the same area, movement of materials to the point of installation, etc. Nonetheless, the intent is to do whatever can be done to get the work ready before the week in which it is to be done.
Sequence: Are assignments selected from those that are sound in priority order and in constructability order? Are additional, lower-priority assignments identified as workable backlog, that is, are additional quality tasks available if case assignments fail or productivity exceeds expectations?
Size: Are assignments sized to the productive capability of each crew or sub-crew, while still being achievable within the plan period?
Learning: Are assignments that are not completed within the week tracked, and the reasons for deviation identified?
Having a plan meet the aforementioned quality criteria is no guarantee for plan success. As mentioned previously, a plan could always fail upon execution. However, the purpose of the Last Planner is to help minimize plan quality failures so that unnecessary execution failures can be avoided. Only assignments that meet these quality criteria may be put on a weekly work plan.
Weekly work plans should not be just a drop-out from a master schedule, but a more detailed schedule considering the actual circumstances. Such detail may be represented at the work package level. Accordingly, it is necessary for a list of work packages that describe a project (SHOULD) to be checked for what CAN be done. The WorkPlan constraint-based database for work package scheduling supports this task.
WORK PACKAGE SCHEDULING
Work Package Definition
Traditionally speaking, ‘‘a work package is a sub-element of a construction project on which both cost and time data are collected for project status reporting. All work packages combined constitute a project’s work breakdown structure’’ (Halpin 1985, p. 154). Work packaging is a planning process that requires a detailed understanding of the scope of the work and constraining factors. Without proper consideration of the constraints, work packages would not be an effective means of managing the job (Kim and Ibbs 1995). However, the literature is vague on exactly how to clearly define a work package’s scope. It is even harder to define what resources are needed to meet those scope requirements. In order to systematically track constraints that may prevent the successful execution of work packages, each work package’s scope needs to be defined clearly.
Our definition of a work package is more production rather than control oriented. A work package defines a definite amount of similar work to be done (or a set of tasks) often in a well-defined area, using specific design information, material, labor, and equipment, and with prerequisite work completed. Grouping similar work allows a continuous flow of resources to be achieved by moving crews from one area to the next. That way, unnecessary interruptions can be avoided. This enables the learning process, which in turn increases productivity (cf. the ‘‘learning curve’’).
It is often assumed in construction that the fastest way to get the job done is to get any work done whenever possible, but this assumption disregards the effort and time that goes into mobilizing and demobilizing for any operation. In order to avoid repeated mobilization and demobilization, an operation should not be started unless it can be finished without interruptions. This criterion helps delimit the amount of work in a work package. Using the Last Planner methodology, operations that span more than a week should be divided up in units that take one week or less to complete, so that work package completion at the end of the week can be statused [see later discussion of Percent of Planned Completed (PPC)]. The units then must be sequenced to maintain continuity of the operation.
The main objective for the development of the WorkPlan constraint-based database for work package scheduling is to allow close monitoring of work packages so that production-level planning according to the Last Planner method can be achieved.
Work Package Features
A work package has constraints that must be satisfied in order for it likely to be carried out successfully and without interruptions. Information regarding these constraints is equally important as the early and late start and finish date, as well as the cost of an activity. Since constraints are specific to each work package, they should be tracked as part of the work package information. These constraints are categorized in five types, as constraints on contract, engineering, material, labor, equipment, and prerequisite work.
Contract: Is this work package in the contract? Is it the result of a newly-issued change order? Has the client approved this work? Has all coordination information been confirmed? Has the subcontract been issued?
Engineering: Have all submittals been turned in? Have all submittals been approved? Have all shop drawings been turned in? Have they all been approved? Are there any outstanding requests for information (RFIs)? Have all methods and procedures been decided? Have special permits that may be required been secured? Have assembly drawings been received?
Materials: Have all fabrication drawings been produced? Have all material requirements and sources for procurement been established? Have all requests for quotation (RFQs) been sent? Have all materials been purchased? Have all materials been fabricated? Have all the materials been delivered? Have all the materials been allocated?
Labor and equipment: Has the work package been scheduled? Are the required laborers available for the duration of the work? Is the required equipment available for the duration of the work?
Prerequisite work and site conditions: Has all prerequisite physical work been completed? Have all work areas been cleared so that the work package can begin? Is adequate storage space available to stage materials? Is the site readily accessible? Are weather forecasts compatible with work requirements?
Even though a specific work package may require constraints in addition to those listed, at least the most frequently recurring constraints have been covered here. The length of our list indicates that the amount of work that goes into preparing a work package is large and possibly more involved than performing construction itself. If any of these constraints is not met for a specific work package, that work package should not be started or its execution will likely be slowed down or interrupted during construction. As part of the Last Planner’s quality criterion for soundness, all constraints must be satisfied prior to the release of a work package to the site for construction.
In the best of circumstances, more work packages will have been released than can be scheduled by the Last Planner. This creates ‘‘workable backlog,’’ namely work the crew will be able to perform should they finish early with all work assigned to them, or should some of the assigned work fall through due to unforeseen circumstances. The crew foreman can then judge how to sequence work and select appropriate work methods, given the crew’s best abilities and capacity limitations (factors of no direct concern to project managers).
Fig. 3 shows the structure of work packages as they have been implemented in WorkPlan. On the left side are the constraints that were enumerated. At the top are the resources being considered in WorkPlan. At the bottom is accounting-related data pertaining to the work package, including cost-to-date and forecast-to-complete. Forecast-to-complete describes in monetary terms the number of hours of labor and equipment that the Last Planner expects to need to complete the work, counting from the date of schedule updating onward. It bears no direct relationship to the allocated budget or a numerical average of past cost or schedule performance, but should reflect only remaining work to be done given the actual site conditions anticipated. The Last Planner’s objective is to get work done as efficiently as possible, which may or may not be possible within the budgeted amount of money and time. In contrast, traditional control systems usually compute forecast-to-complete based on actual-cost-to-date or actual-schedule-to-date. Forecast-to-complete then is either an extrapolation of the average throughout the project or the average over a certain number of weeks based on progress-to-date. This method tends to encourage crews to select work based on how progress is measured (earned value), rather than allowing them to get the entire job done efficiently.
On the right side of Fig. 3 is the derived information, including timesheets, the cost report, and the PPC report. PPC can be calculated by dividing the number of completed assignments by the total number of assignments each week (Ballard and Howell 1994a,b, 1998).
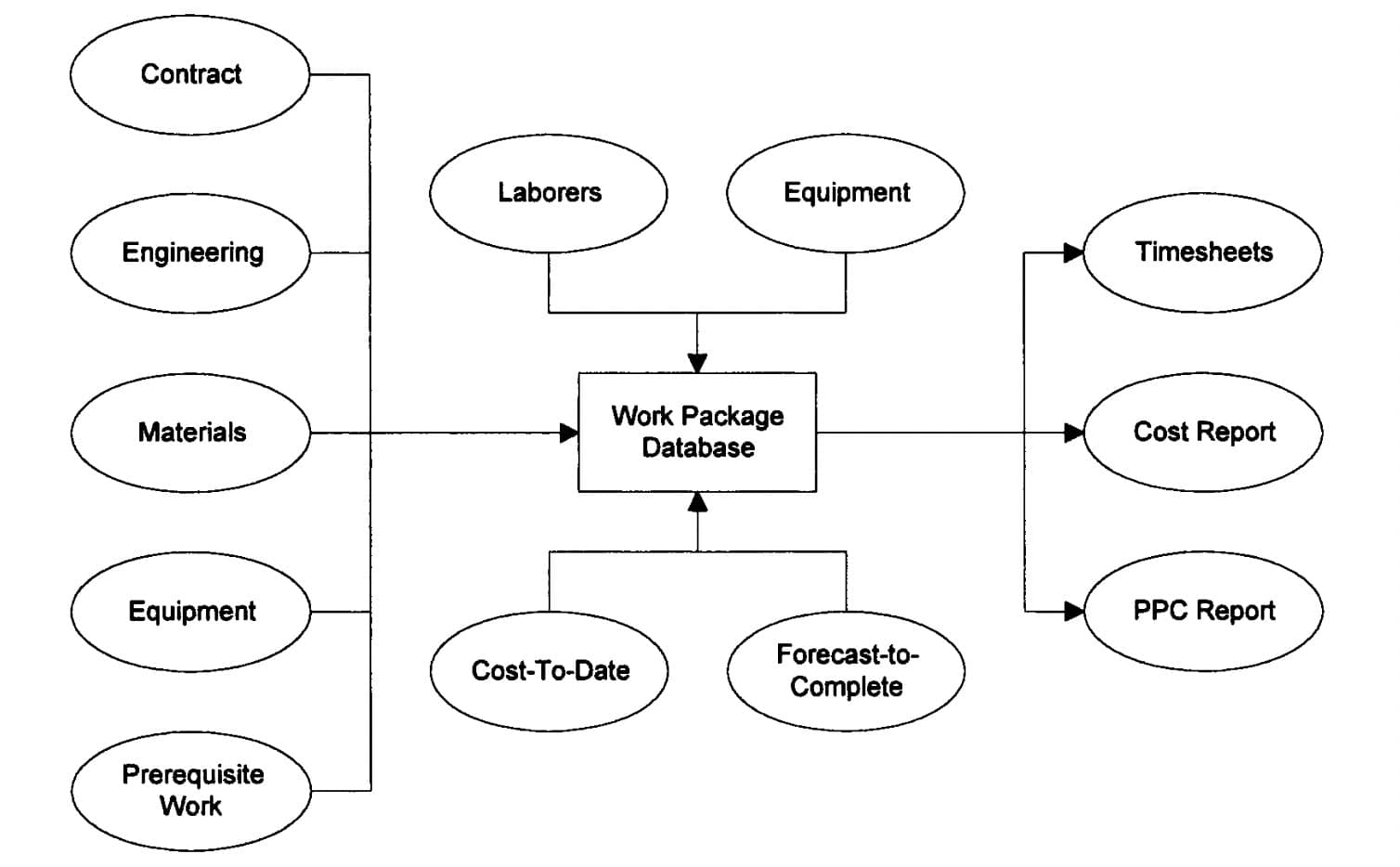
It is a measurement used to gauge the reliability of the planning system. PPC must be tracked not only by recording work-packages’ completion status, but also be elaborating on reasons for failure to complete the work as planned. This may be of value in the future elaboration of constraints and it also enables learning.
IMPLEMENTATION OF WORKPLAN
In the application, the weekly work plan is generated using a database. This database has information about the work packages to be done and resources that can be used, i.e., the laborers and the equipment within the company. Electronic formats of this information usually exist in the company whether it is in spreadsheets or word processor files. In WorkPlan, this information can be captured and used throughout the project—a technique ‘‘capture information once and at the source’’ recommended by process reengineering (Hammer 1990).
Generating a weekly work plan on a computer not only saves time, but it can also prevent errors. A real-time cost generation function can compare alternative resource allocations. A cross-allocation checking function can detect resource conflicts (assignment of the same resource to different work packages at the same time) before they arise on the site.
Since construction information presents itself in groupings of similar data that are tightly interlinked, a database provides a perfect platform for application development. From the variety of database management systems on the market, Microsoft Access 7.0 was chosen because it can be easily programmed through Visual Basic for Applications. It was also chosen because the program can be distributed with the runtime version of Access so that users do not have to purchase Access to run the WorkPlan database. Since specialty contractors are the main users of this application, affordability was one criterion for software platform selection.
Work package data are the basis upon which all other data are built. The Work Package Entry Form allows users to enter information about the work package’s number, project number, description, duration, and budget cost (no figure shown). In the same manner, information about labor and equipment is input (Fig. 4).
For each work package input by the user, WorkPlan generates five categories of constraints by default that refer to: (1) contract; (2) engineering; (3) materials; (4) labor and equipment; and (5) prerequisite work. Fig. 5 shows how the program user can detail the problems and solutions for each category. The problems may be selected from the preloaded list (see section ‘‘Work Package Features’’) or be written in by the user if items need to be added or other wording is found to be more appropriate. At the bottom of this screen are problems that are still outstanding, and at the top of the screen those that have been solved. Once an outstanding problem has been solved (checked), it automatically moves up to the top. Solved problems are not deleted from the database even though they require no further attention. Keeping them displayed confirms they have been attended to. The list of solved problems can also be used to construct a knowledge base of constraints to help anticipate problems with similar work in the future.
Once all constraints for a work package are satisfied, the work package can be released for construction. WorkPlan displays unreleased work packages at the top of the Work Package Release screen and displays released work packages at the bottom of the same screen (no figure shown). By pressing the down-arrow button, an unreleased work package can be released; by pressing the up-arrow, a released work package can be unreleased. The latter should occur in exceptional circumstances only, if a previously unidentified constraint crops up at the last minute or a constraint is not satisfied to the extent it was anticipated.
The Resource Assignment Screen (Fig. 6) allows the Last Planner to schedule a released work package. Only released work packages can be scheduled for execution and have resources assigned to them. As shown in this screen capture, the names of laborers and equipment to be assigned to a specific work package are selected from a drop-down list using data stored in the database. The hours represent the time each resource will work on the specific work package.
Once the schedule is set, WorkPlan checks the total number of hours committed for each resource across all work packages of all projects. It notifies the Last Planner if any resource is assigned for more than 8 h/day, which is assumed to be a full working day. If overtime is intended, then WorkPlan will apply the corresponding charges. If overtime is the result of oversight, the Last Planner must revisit the work packages involved and reassign resources to balance them more evenly.
‘‘Remaining Work’’ is used in estimating the total cost of the work package based on the expected unit cost and quantity of work that is left to be done.

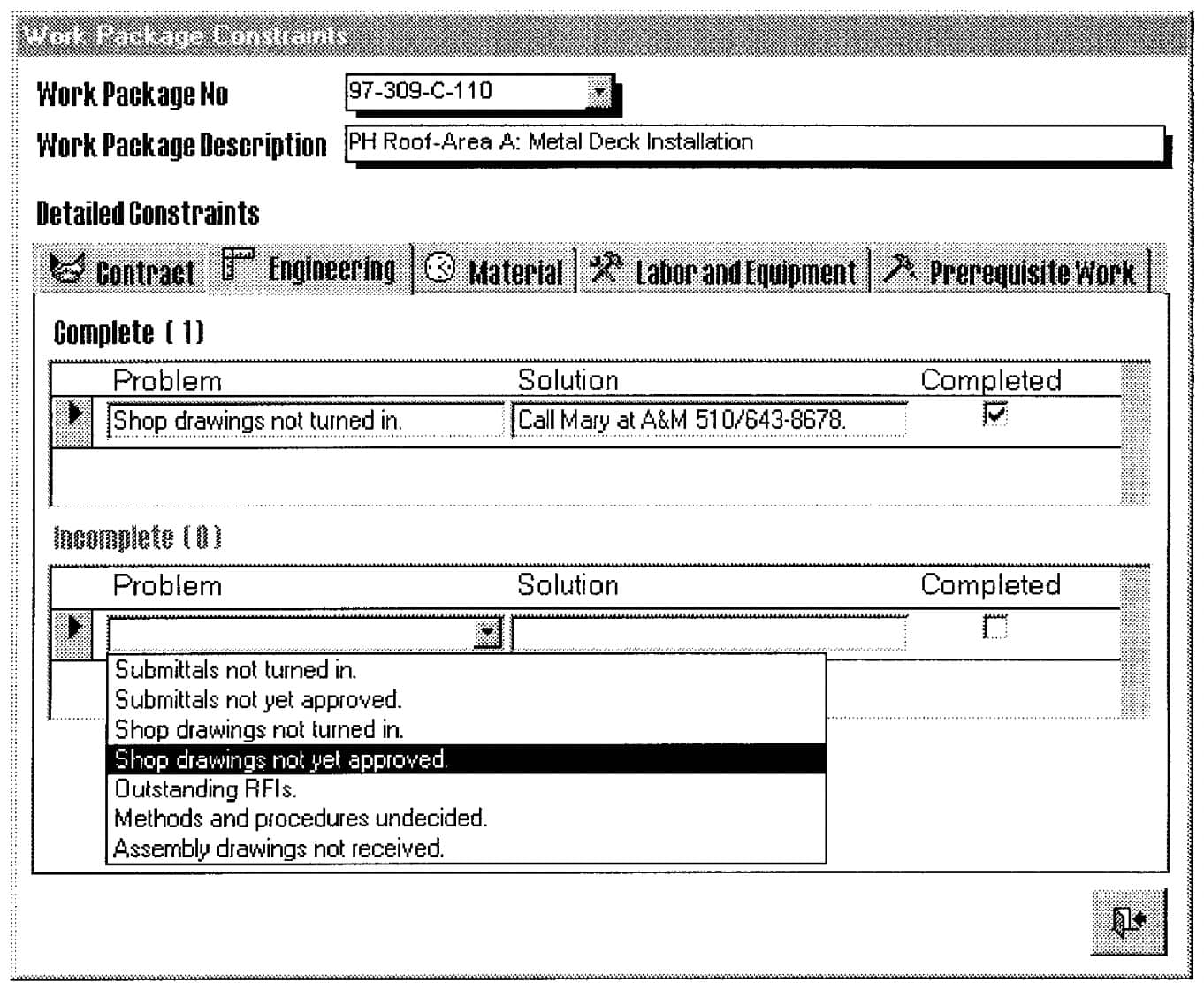
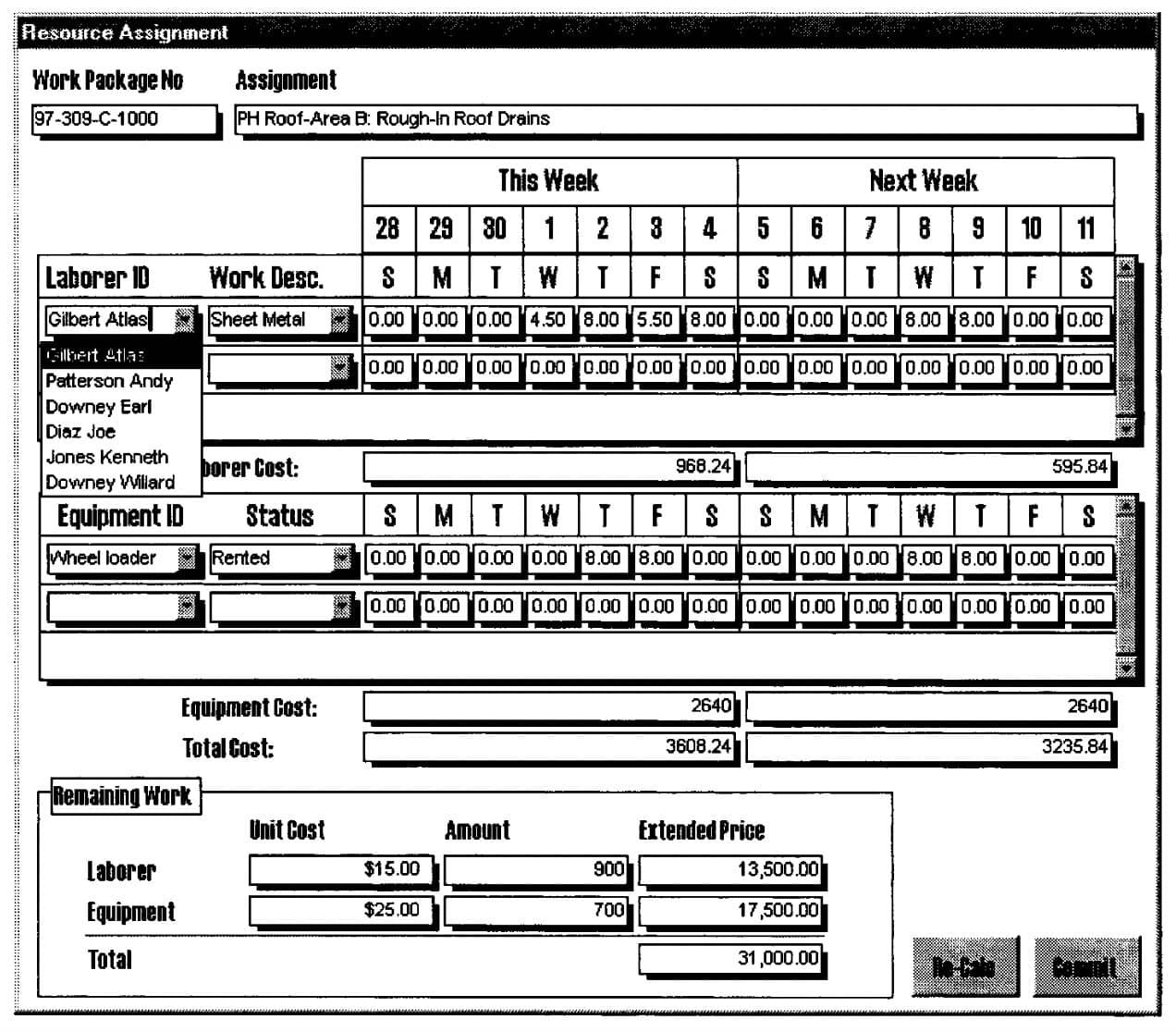
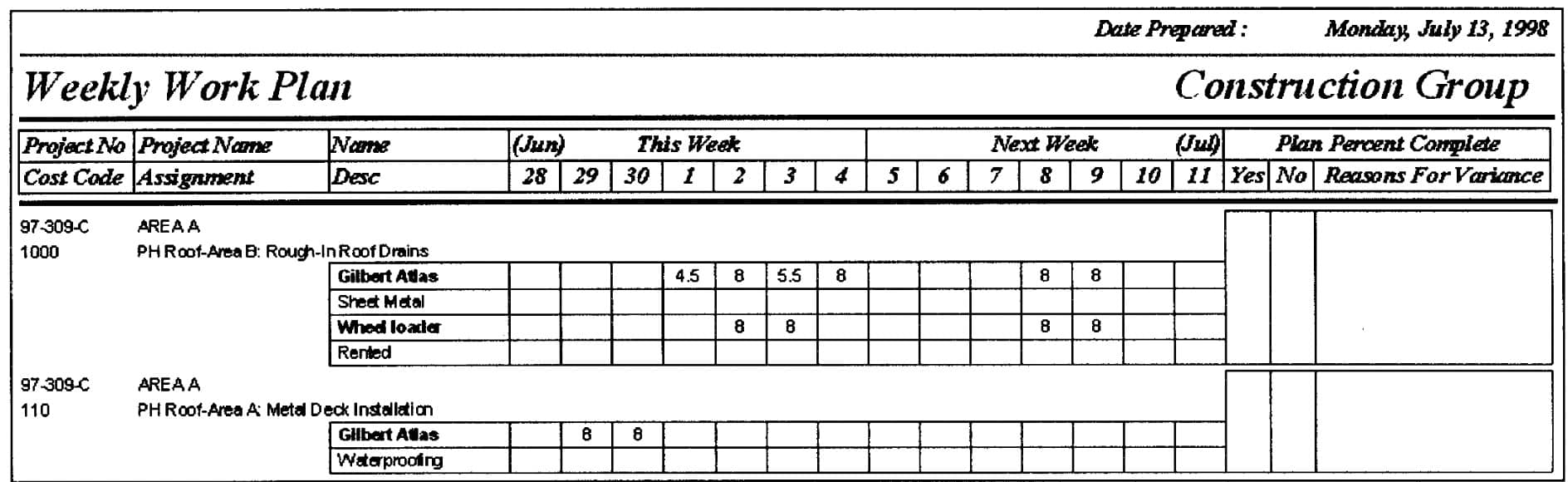
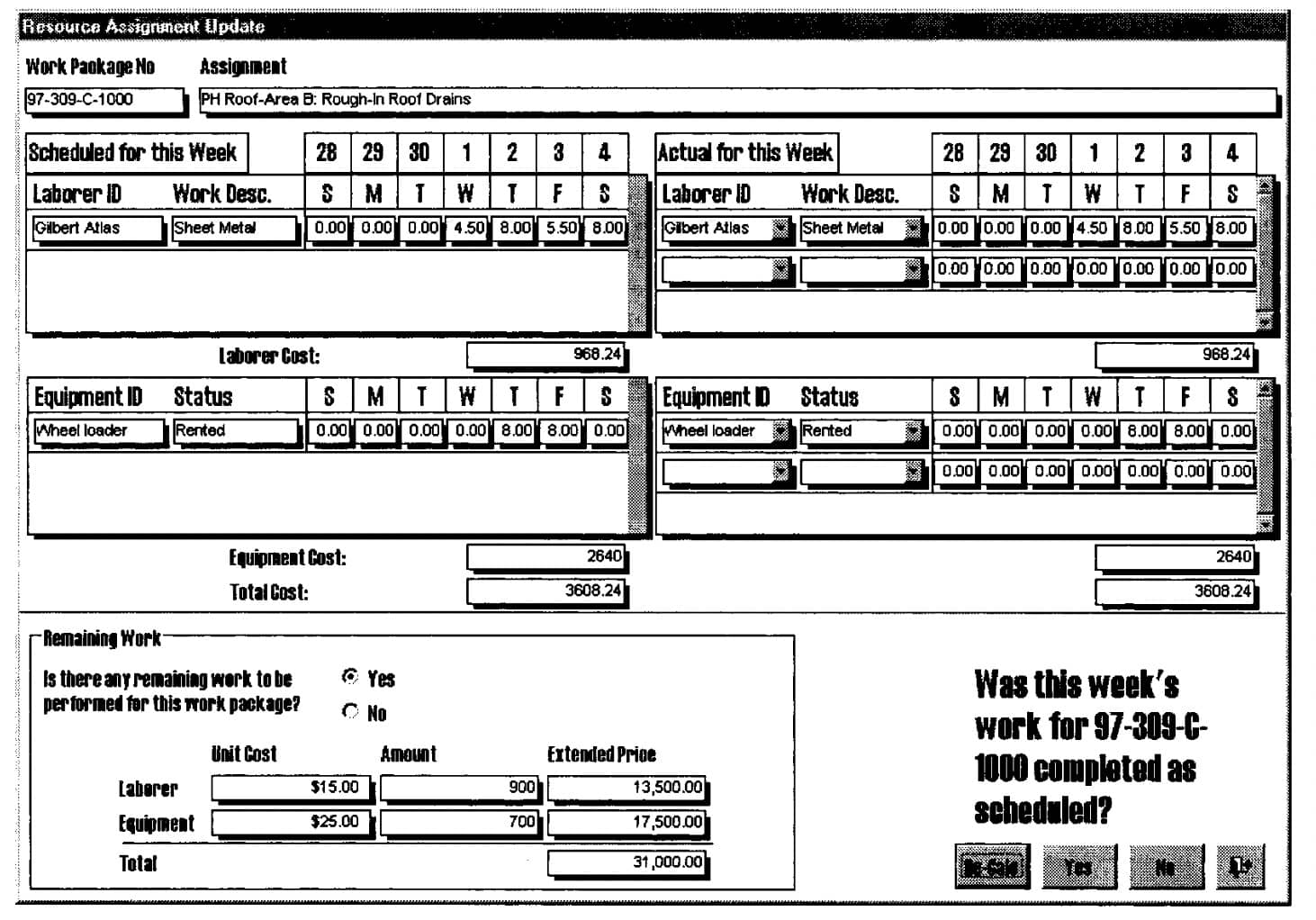
Every time the schedule is modified, the Last Planner has the option of updating the estimate of the remaining work. This information is not generated within the database. It is based on the Last Planner’s estimates based on the amount of work left. By estimating the total cost of each work package, a realistic target cost can be set.
Fig. 7 shows a weekly work plan generated using input from the Resource Assignment Screen. It can be printed out and handed to the field crew. Once a work package has been completed, the crew is expected to fill out the actual number of hours they worked on each specific assignment and check whether or not it was completed as planned. If not, they must provide reasons for variance. This data is then entered into the computer by means of the Resource Assignment Update Screen.
The Resource Assignment Update Screen (Fig. 8) represents the scheduled work at the left side and allows for user input of the actual schedule at the right side. The default value of the right side is ‘‘as scheduled.’’ Changes can easily be made by selecting resources from the drop-down list and typing the number of hours worked. The update can be used to generate timesheets, if needed for accounting purposes. Tracking this information provides the basis for the cost calculation and, more importantly, allows for measurement of the reliability of the current scheduling system.
The ‘‘Remaining Work’’ appears as it did on the Resource Assignment Screen, that is, WorkPlan does not recalculate the value in any way. Updates must be entered explicitly by the Last Planner. The option button to record the completion of the work package lets the planner specify that the work package for the whole project is complete and therefore can be removed from the list of work that is ready to be carried out (workable backlog).
After recording the information, reasons for variance (difference between ‘‘scheduled’’ and ‘‘actual’’) are input (Fig. 9). These reasons are divided into seven categories, namely: (1) contract; (2) engineering; (3) material; (4) labor and equipment; (5) prerequisite work; (6) weather; and (7) accident. In turn, WorkPlan uses this data to create the PPC report that represents the reliability of the current planning system (Fig. 10). The vertical axis on the left shows the PPC. The axis on the right is for the number of occurrences of reasons for each category. The solid graph line represents PPC and the bars correspond to the number of occurrences. The occurrences can be used for deciding where to focus management attention in order to improve the reliability of the planning system.
If desired, WorkPlan can generate a timesheet, grouping actual work completed by the laborer and total wages for each laborer by work package. Another useful report is a listing of work packages per project, presenting a high-level view of what the project entails.
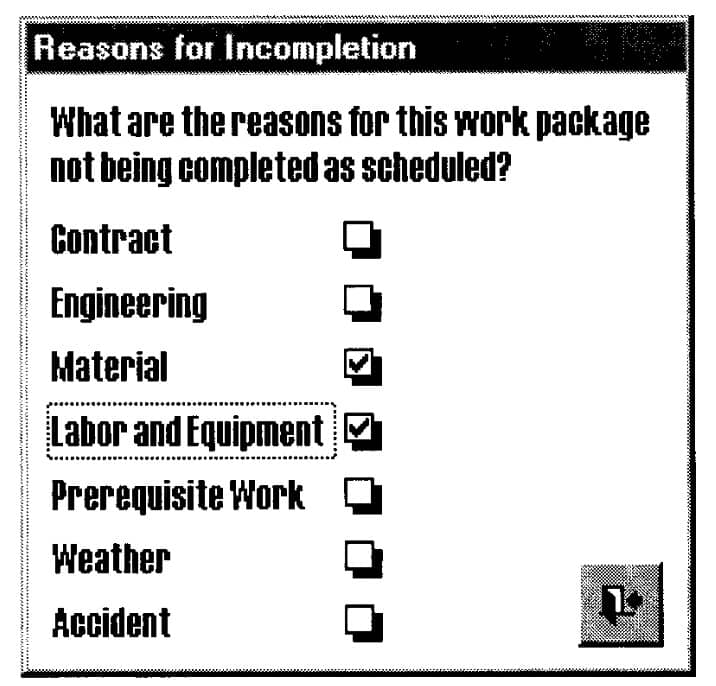
RELATED WORK
Many planning systems exist that use CPM, such as Primavera Project Planner (Primavera 1997) and Microsoft Project (Microsoft 1997). These traditional systems are based on a purely hierarchical top-down approach where every activity is broken down into smaller ones, each one having a single parent. General contractors prepare executive level schedules to cover the entire project duration. In turn, their superintendents create lookahead schedules that reveal more detail on activities to be executed in the near future (typically up to 3 or 4 weeks out). Specialty contractors then prepare their own schedules to meet the project’s needs. In turn, their crews detail actual work in weekly work plans.
Fig. 11 shows the CPM schedules of two projects, each performed by a different general contractor, but a single specialty contractor ‘‘SC 1’’ (shown by the cross-hatched activity) performing part of the work in both. Even though a specialty activity may be unique in each project (activity ‘‘a’’ in ‘‘Project A’’ and activity ‘‘b’’ in ‘‘Project B’’), the work requires the repeated application of a specialty for ‘‘SC 1’’. The specialty contractor therefore tries to schedule work in a continuous flow, whereas the general contractor will schedule a sequence of dissimilar pieces of work. These tasks significantly differ from one another so that different (computer) support tools are needed.
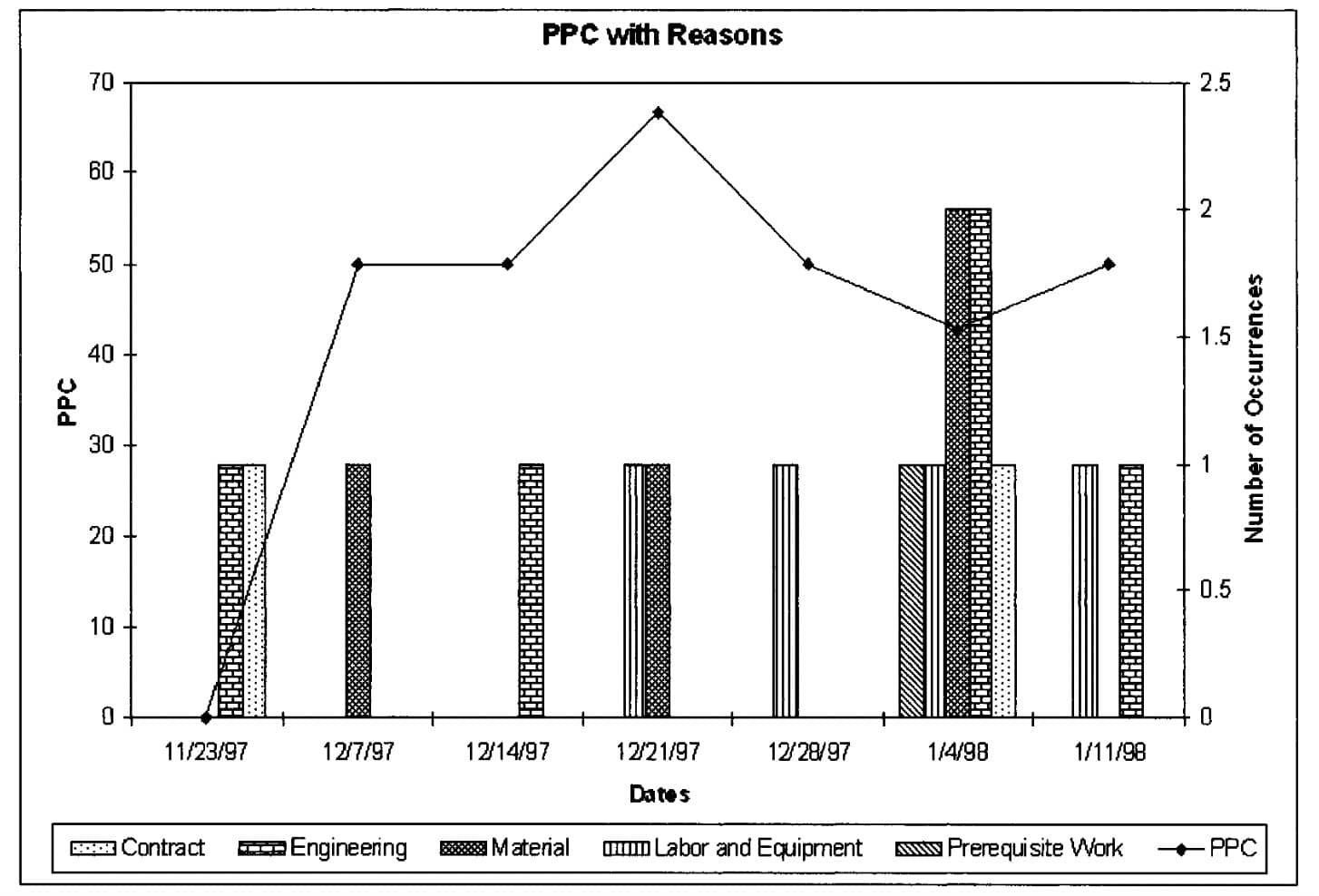
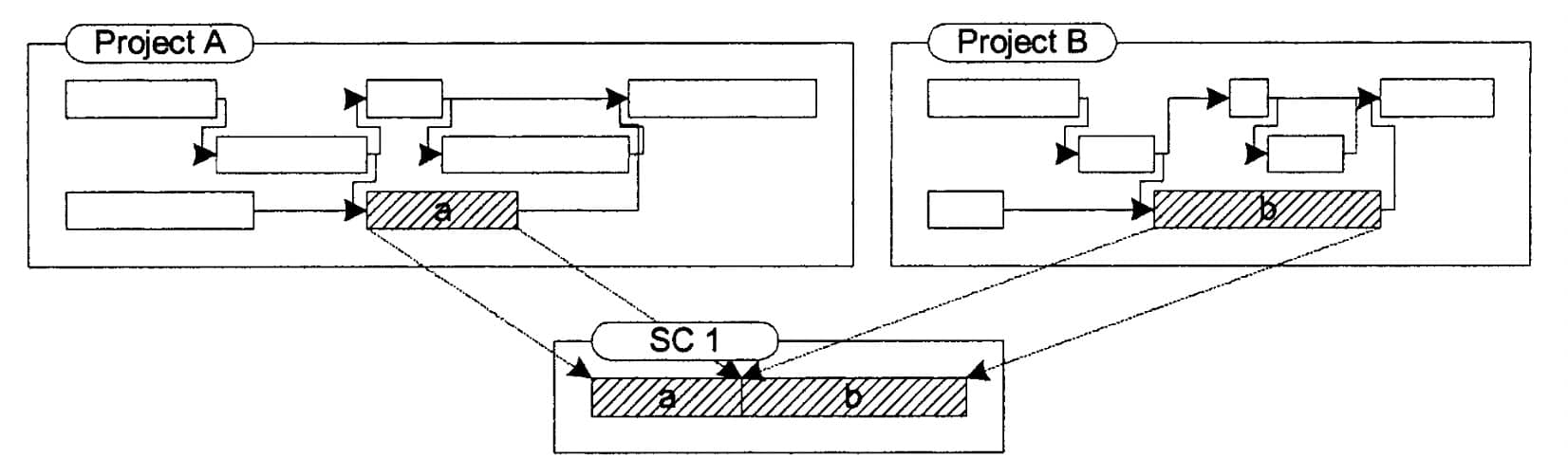
Each specialty contractor’s detailed design, fabrication, procurement, and construction process tends to take the form of a job shop (Tommelein and Ballard 1997) as is common in manufacturing, where the products are made to fulfill particular customer orders. This view differs from the project view adopted by general contractors and reflected in existing CPM software. CPM focuses on the project itself, which has a definite start and finish date, in turn making it possible to compute activity float and then level resource histograms by taking ad- vantage of it. By contrast, job-shop scheduling focuses on the continuous flow of work (jobs), where jobs have due dates but their execution may be interwoven so that there is no clear start or finish for the shop’s operation as a whole. Shop capacity tends to be a given, however, and it is therefore critical to maintain a steady flow of work for all resources. This is achieved by creating a workable backlog. Float then becomes a secondary issue provided that the shop has adequate capacity to perform all scheduled work. WorkPlan’s scheduling method supports job-shop scheduling where the available resources are known and the work-to-be-done is matched to keep them productive. WorkPlan supports the flow of information by making all constraints explicit in the planning phase.
Quite a few commercial database packages exist to track RFIs, submittals, drawings, etc. Examples are Expedition (Expedition 1997) and ProLog (Prolog 1998). WorkPlan also differs from these systems in that it adopts a work package view, that is, all record keeping is structured in function of what may constrain the execution of a work package. WorkPlan database relations thus reflect constraints. By systematically checking all constraints before work packages are released to construction, one can avoid making low-quality assignments, thereby increasing reliability in the construction process. Re- liability is a key aspect of lean production theory (Howell and Ballard 1994).
Application of the lean production theory in construction was prompted by the theory’s success in manufacturing and the appeal of its emphasis on the management of flow in production and generation of value (Koskela 1992; Womack and Jones 1996; Alarcon 1997). A number of studies have been conducted to date in order to refine the thinking process and develop methods to implement lean production in construction. However, no computer tools have yet been developed for field-level use. Several of the lean production techniques identified by Womack and Jones (1996) have been implemented in WorkPlan:
Clearly documenting, updating, and constantly reporting the status of all process flows to all involved, so each person knows what others do and understands the implications of the quality of their own work on the quality of the process output.
WorkPlan stores all information in a database and generates relative information from it.
Synchronizing and physically aligning all steps in the production process so there is little wait time for people or machines, and virtually no staging of partially completed products.
WorkPlan tries to eliminate unnecessary waiting times on the site by screening work packages (Ballard and Howell 1998). Releasing work packages only when all resources are ready allows construction to be carried out with a minimum chance of being interrupted. As a result, fewer partially com- pleted work packages are on site.
Stopping the assembly line to immediately repair quality defects. This usually is very disruptive for the process as a whole, but there are several advantages to doing so: (1) the flawed processing step can be corrected right away, before numerous other assemblies have undergone the same treatment, resulting in additional defects; and (2) it is substantially easier and less costly to discover and re- pair a quality defect early on in a process rather than at the end, after an assembly has been completed.
WorkPlan makes it possible to identify defects readily (i.e., reasons for deviation from the schedule) so that the scheduling process can be rectified immediately in order to prevent the same defect from reoccurring.
In its present implementation, WorkPlan does not treat materials as a separate resource to be allocated though material availability can be modeled as a constraint. This omission is intentional. A concurrent research project will result in the development of a tool to manage data pertaining to the materials supply chain (Sadonio 1998; Sadonio et al. 1998). This tool, named CADSaPPlan (Computer Aided Design, Sourcing, and Procurement Planning), is to feed WorkPlan data on materials availability on site, expected delivery dates, lead times, etc.
SUMMARY
Existing CPM-based project management tools used in construction do not provide appropriate support to field crews in production scheduling. They do not help shield crews from uncertainty and provide no insight into resource availability. As an alternative, the Last Planner approach to scheduling was presented, where work package information is tracked with the necessary detail to plan and control on-site production. Traditional CPM-based tools release to construction what SHOULD—instead of what CAN—be done. They essentially provide support during project preplanning (i.e., planning prior to the start of construction), but not during construction when actually-needed resource levels differ from those anticipated and available. In contrast, the Last Planner implemented in the WorkPlan computer tool provides a method to systematically check resource availability. This level of planning must be performed on any project, large or small, by the crew that will execute the work.
WorkPlan guides the user step by step through the process of spelling out work packages, identifying constraints, checking constraint satisfaction, releasing work packages, and al- locating resources; then at the end of the week, collecting field progress data and reasons for plan failure. WorkPlan not only allows detailed scheduling of work packages, it also integrates various kinds of construction data so that the relationships be- tween them are easy to see. This systematic approach helps users work more accurately and saves time when creating quality work plans. It also helps users learn from understand- ing reasons for failure.
The WorkPlan system is straightforward in concept and implementation. Though using WorkPlan requires a different mind set than is common in current project management practice, the tool is valuable for keeping track of a large amount of tedious details describing resources, that, when not avail- able, could seriously hamper the productivity of field crews.
ACKNOWLEDGMENTS
The implementation of WorkPlan was initiated with funding from the University of California, Berkeley. Further research to expand its capabilities is being funded by grant CMS-9622308 from the National Science Foundation whose support is gratefully acknowledged. Any opinions, findings, conclusions, or recommendations expressed in this paper are those of the authors and do not necessarily reflect the views of the National Science Foundation.
FOOTNOTES
PhD Student, Constr. Engrg. and Mgmt. Program, Dept. of Civ. and Envir. Engrg., 215 McLaughlin Hall #1712, Univ. of California, Berkeley, CA 94720. E-mail: choohj@ce.berkeley.edu
Assoc. Prof., Constr. Engrg. and Mgmt. Program, Dept. of Civ. and Envir. Engrg., 215 McLaughlin Hall #1712, Univ. of California, Berkeley, CA. E-mail: tommelein@ce.berkeley.edu
Lect. at Univ. of Calif., Berkeley, and Res. Dir., Lean Construction Inst., 4536 Fieldbrook Rd., Oakland, CA 94619, E-mail: ballard@ce.berkeley.edu
Pres., Pacific Contracting, Inc., 222 Sutter Street, Ste. 310, San Francisco, CA 94108. E-mail: trz@pacificcontracting.com
Note. Discussion open until November 1, 1999. To extend the closing date one month, a written request must be filed with the ASCE Manager of Journals. The manuscript for this paper was submitted for review and possible publication on September 12, 1998. This paper is part of the Journal of Construction Engineering and Management, Vol. 125, No. 3, May/June, 1999. qASCE, ISSN 0733-9634/99/0003-0151 – 0160/ $8.00 1 $.50 per page. Paper No. 19246.
APPENDIX. REFERENCES
Alarcon, L., ed. (1997). Lean construction. A. A. Balkema, Rotterdam, The Netherlands, 497.
Ballard, G., and Howell, G. (1994a). "Implementing lean construction: Stabilizing work flow." Proc., 2nd Annu. Conf. on Lean Constr., Pontificia Universidad Catolica de Chile, Santiago, Chili, Sept., http://www.vtt.fi/rte/lean/santiago.htm. Reprinted in Alarcon (1997).
Ballard, G., and Howell, G. (1994b). "Implementing lean construction: Improving downstream performance." Proc., 2nd Annu. Conf. on Lean Constr., Pontificia Universidad Catolica de Chile, Santiago, Chili, Sept., http://www.vtt.fi/rte/lean/santiago.htm. Reprinted in Alarcon (1997).
Ballard, G., and Howell, G. (1998). "Shielding production: An essential step in production control." J. Constr. Engrg. and Mgmt., ASCE, 124(1), 18 – 24.
Expedition 5.1. (1997). Primavera Systems Inc., Bala Cynwyd, Pa.
Goyen, J., and Ballard, G. (1996). Internal publication by Brown & Root, Inc., supporting the Last Planner initiative. Houston, Tex.
Halpin, D. (1985). Financial and cost concepts for construction management. Wiley, New York.
Hammer, M. (1990). "Reengineering work: Don't automate, obliterate." Harvard Business Rev., July – August, 104 – 112.
Howell, G., and Ballard, G. (1994). "Lean production theory: Moving beyond 'can-do'." Proc., 2nd Annu. Conf. on Lean Constr., Pontificia Universidad Catolica de Chile, Santiago, Chile, Sept., www.vtt.fi/rte/lean/santiago.htm. Reprinted in Alarcon (1997).
Kim, J.-J., and Ibbs, C. W. (1995). "Work-package — Process model for piping construction." J. Constr. Engrg., and Mgmt., ASCE, 121(4), 381 – 387.
Koskela, L. (1992). "Application of the new production philosophy to the construction industry." Tech. Rep. No. 72, Center for Integrated Facilities Engineering, Dept. of Civil Engineering, Stanford University, Stanford, Calif.
Microsoft Project ’98. (1997). Microsoft Corp., Redmond, Wash.
Primavera Project Planner 2.0. (1997). Primavera Systems Inc., Bala Cynwyd, Pa.
Prolog Manager. (1998). Meridian Project Systems, Inc., Sacramento, Calif.
Russell, A., and Froese, T. (1997). "Challenges and a vision for computer-integrated management systems for medium-sized contractors." Can. J. Civ. Engrg., 24(2), 180 – 190.
Sadonio, M. J. (1998). "CADSaPPlan: The Last Designer’s CAD-database system that integrates Sourcing, Design, and Procurement Planning." M. Engrg. Rep., Constr. Engrg. and Mgmt. Program, Civ. and Envir. Engrg. Dept., University of California, Berkeley, Calif.
Sadonio, M., Tommelein, I. D., and Zabelle, T. R. (1998). "The Last Designer’s Database-CAD for Sourcing, Procurement, and Planning." Proc., Computing Congr. ’98, ASCE, 364 – 375.
Tommelein, I. D., and Ballard, G. (1997). "Coordinating specialists." Tech. Rep. No. 97-8, Constr. Engrg. and Mgmt. Program, Civ. and Envir. Engrg. Dept., University of California, Berkeley, Calif; also, Proc., 2nd Int. Seminar on Lean Constr., October 1997, A. S. I. Conte, Logical Systems, Sa˜o Paulo, Brazil.
Womack, J. P., and Jones, D. T. (1996). Lean thinking: Banish waste and create wealth in your corporation. Simon and Schuster, New York.