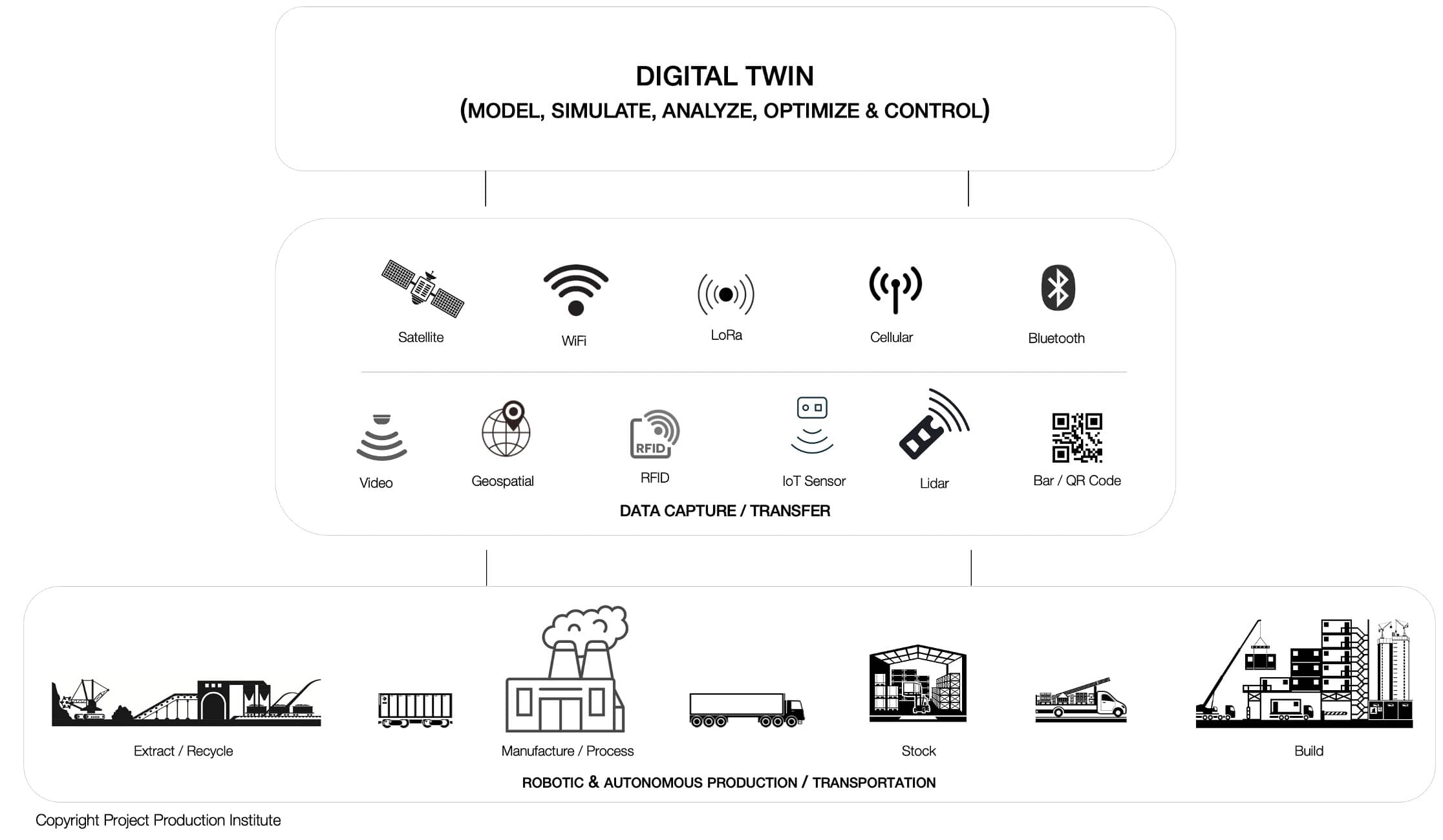
COVID 19, the war in Ukraine, industrial action at ports and several other factors, are causing supply chain challenges across all industries including engineering and construction. Additionally, project supply chains are known to be inherently complex and dynamic. Project performance depends highly on how efficient and effective supply chains are throughout the project delivery process. It is therefore essential to establish and create a common understanding of what it means to configure and operate project supply chains efficiently and effectively.
But first, let’s establish some common ground about what we mean by supply chains in the context of projects. Supply chains are best understood as a system of interconnected production and inventory systems that provide the needed materials and services to the project. Configuration decisions include decisions related to what to buy from external suppliers and service providers, what to make internally, how to make it, who should make it and where should it be made. Some even include what should be made (supply chain considerations during design or product development).
In addition to other attributes that may be of value to a specific situation, the minimum requirements for an effective supply chain include:
Reliability: Inbound resources must be delivered when needed and in accordance with quality specifications. In advanced industries such as automotive, OEM’s work in partnership through supplier development programs to ensure suppliers are able to meet technical and supply volume requirements. Improving product and process design, reducing lead time, and improving quality are all elements of these programs. This PPI paper, “Consequence of Lead Time of Capital Projects”, provides a framework for collaborating with suppliers to compress lead time, enhance reliability and reduce cost.
Transparency: Consumers can see at any given time when inbound products will arrive and if there will be deliveries that arrive too early or too late. The advent of the IoT (Internet of Things) technology enabled by edge computing, AI/ML, and increased use of satellites, offers a significant improvement in transparency over the supply chains of the past. The use of these technologies enables real-time location and environment tracking for better control of the supply process as depicted in the schematic below for Intelligent Production.
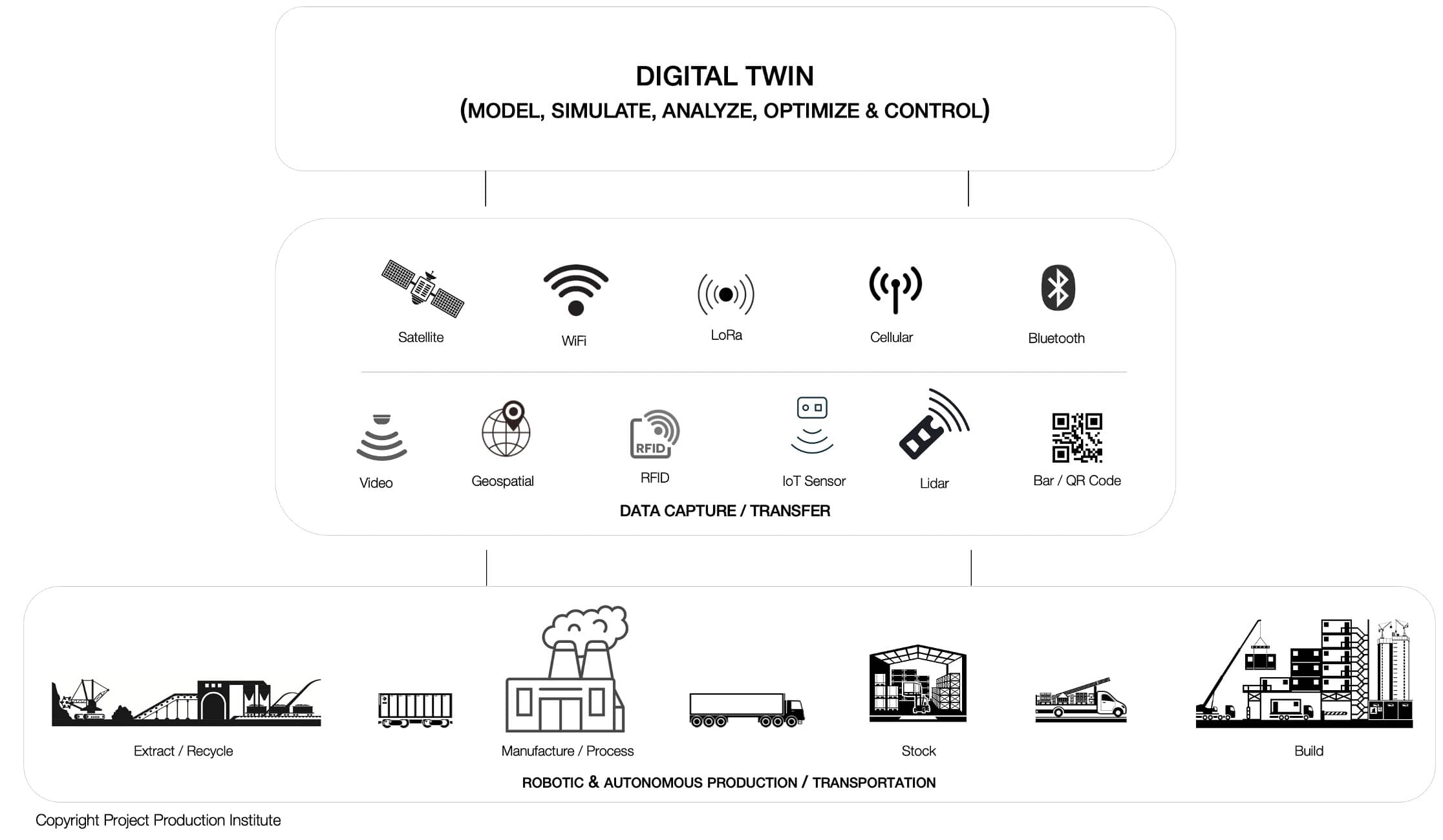
Redundancy: Measures should be in place to protect any disruption resulting from geopolitical issues, industrial actions, revisions in demand for material or part, and many other sources. For instance, Toyota Motor Corp. is well known for the use of two suppliers in most categories with one supplier receiving 80% of the volume and the other 20%. At one large infrastructure project, raw materials were shipped by rail. But, in order to mitigate risk of supply disruption related to industrial action or railway maintenance, a trucking company was paid a fair sum to be on call to provide trucks if needed. The small sum paid to the trucking company paid for itself when a single disruption occurred.
Agile / Flexible: Demand often changes for a variety of reasons. An effective supply chain must be able to adopt to these changes in demand without experiencing excessive cost. To achieve agility and increase flexibility, excessive amounts of inventory in the supply chain must be identified and removed. Inventory includes WIP and stocks. Any inventory can increase the time required to make changes. Additionally, buffer strategies including what type of buffer is adequate (capacity and/or inventory), along with where in the supply process buffers are placed and how much, must also be carefully considered.
Cost Efficient: Supply chains must operate efficiently and at best value. This can only be achieved through an end-to-end value stream perspective, where supply is seen as a dynamic system, not a transaction. The use of various production system modeling, simulation and analysis methods and tools provide the means for identifying and optimizing supply chain efficiency.
None of this is possible if the supply chain does not have the right amount of capacity and inventory. Inventory includes stock, i.e., what they buy / store, and work-in-process, i.e., what they make.
Too much WIP results in extended cycle times with additional cash tied up and reduced agility. Too little WIP results in insufficient output to meet the demand. Furthermore, too much stock results in unnecessary cash tied up, while not having the right combination, most often results in reduced service levels, even if more than necessary cash is tied up. Too little stock results in delays to project completion.
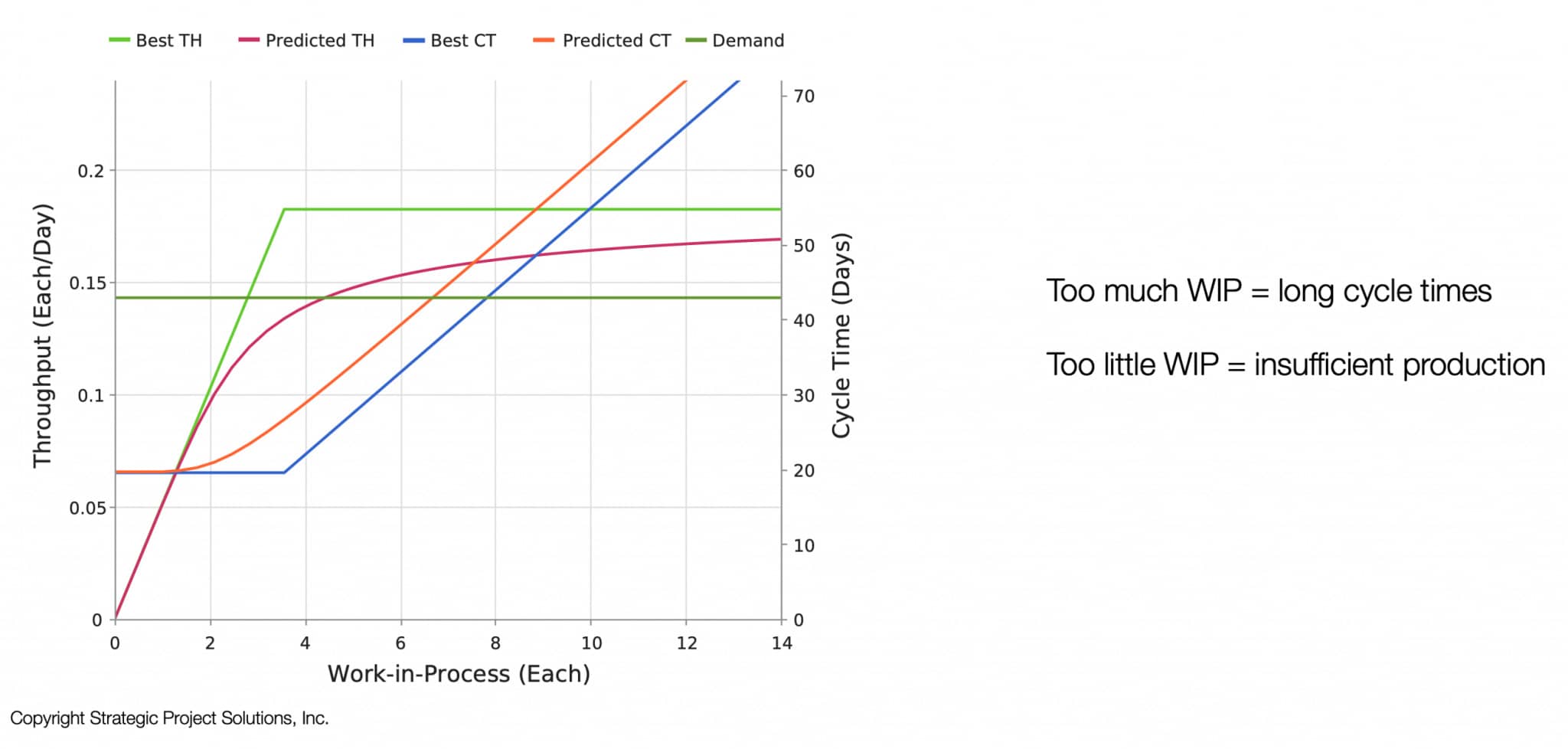
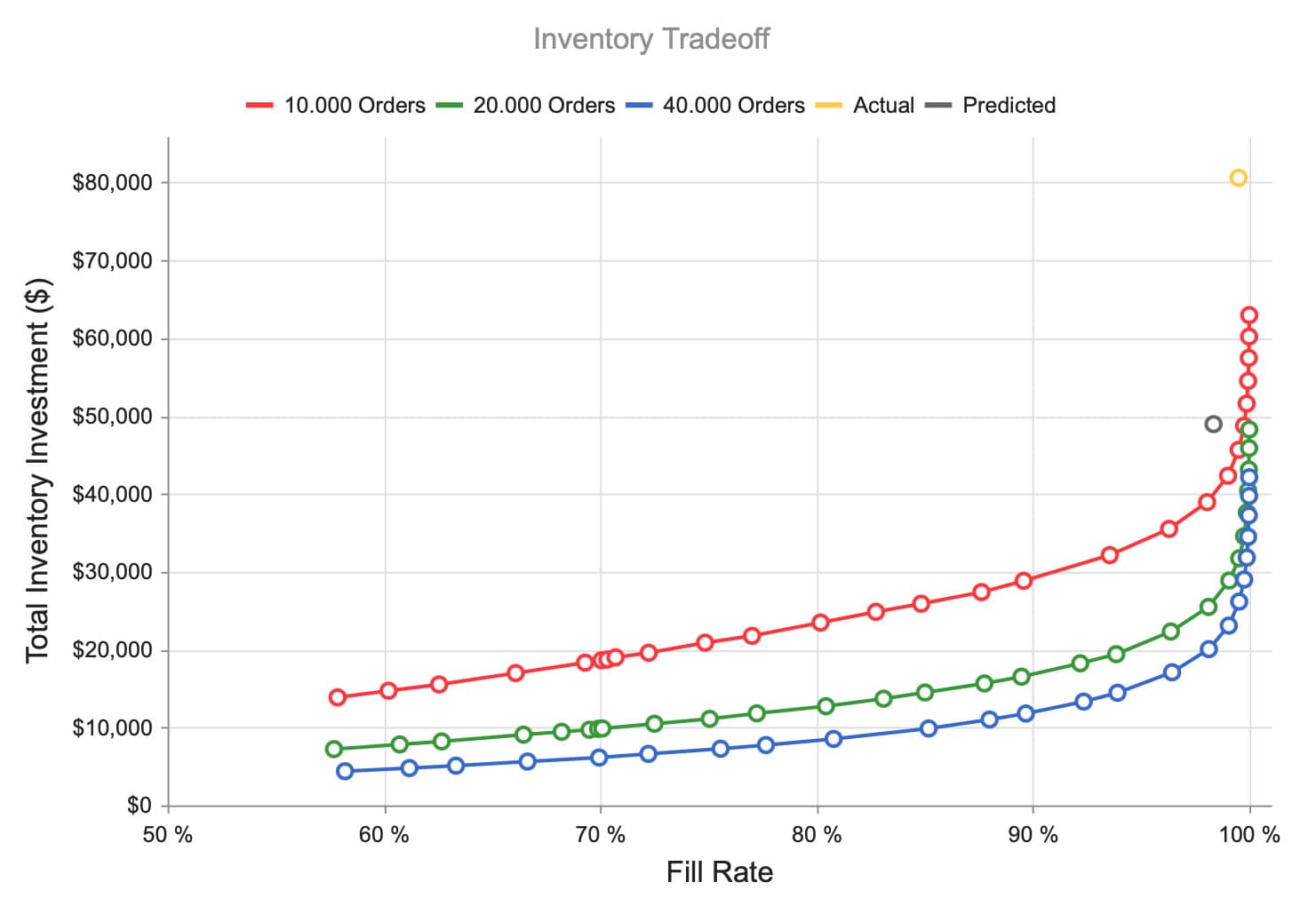
Based on the above attributes, it is important to highlight that efficient and effective project supply chains don’t just happen. There are a series of strategies (e.g., operate based on optimal WIP levels) and methods (e.g., supplier programs, production system modeling) that will enable project teams to ensure their supply chains are reliable, transparent, agile, flexible and are cost efficient.
What are you doing now to make your supply chains efficient and effective?